Establishing an efficient prototype and small batch electronic package production line is not an easy process. This is largely due to the need to make the right decisions on tools and equipment that take into account the specifics of this business.
Small batch and prototype production in industrial plants is often dependent on either main line capacity or subcontractors. Therefore, this type of work is prolonged or unprofitable while waiting for the right moment. Large companies to remain competitive often decide to create separate lines for independent implementation of these processes. At the same time, many new entrepreneurs – often operating in the form of startups – are just starting out in the electronics industry with this type of production.
Quite obviously, the selection of appropriate equipment and solutions can be crucial to the future of this project. What becomes clear, then, is the need to make proper, informed decisions based on experience in developing similar projects. The problem arises when the project implementer does not have such experience. In such a situation, the solution may be to partner with a specialized entity.
In Poland, consulting activities in this field are provided by RENEX Group. It is both a manufacturer of its own products intended for the electronics industry and a representative of global brands in this field. In this paper, we will look at selected problems in the creation and operation of prototype and small batch lines as well as solutions available from RENEX.
Space
Designing a small-batch or prototype electronics production line should start with the space in which the activity will take place. Taking into account the low resistance of a large part of the components used in the industry, such assembly – just like high-volume assembly – should take place in an EPA zone, i.e. a space designed and equipped to reduce the risk of damage from electrostatic discharge. This includes the selection of appropriate flooring, furniture as well as equipment and tools.
RENEX Group specializes in consulting on the creation and proper maintenance of EPA zones. Specialists assist in the selection of appropriate solutions, as well as conduct audits and inspections to identify and eliminate possible errors in its operation. The Group is also the manufacturer of REECO anti-static furniture, which is winning global markets. These are modular structures, designed to be adapted to the requirements of a given space. What is important from the point of view of this study, on their basis it is possible to create individualized and ergonomic manual workstations – necessary for making quick corrections in prototypes or small series of products being created. An example of this is the ready-to-implement design – the REECO Premium Antistatic Table – with electrically adjustable tabletop height.
An important element of the EPA zone – although one that is often not seen as its equipment – is also appropriate employee attire. In this case, appropriate can be understood as one that is both comfortable – allowing for comfortable work – and has anti-static properties. Negligence in this regard is often the weak link causing all the efforts put into properly creating and maintaining an ESD zone to be nullified. In this case REECO brand products are worthy of recommendation as well. The range of anti-static clothing, at competitive prices, is very wide, allowing you to choose solutions tailored to the nature of your business.
MANUAL WORKSTATION
The next step in creating a small batch and prototype production line is to properly equip the manual workstation. The foundation – along with small tools such as clippers and tweezers – is a good soldering station. Of great importance is the ability to quickly, and preferably programmably, change the temperature of the soldering tip and the availability of a wide range of compatible soldering tips. Work will be expedited by stations equipped with more than one soldering iron with different tips, so that subsequent tasks can be accomplished without modifying tools.
Such features include, for example, the JBC DDPE Precision – Digital Dual Tool Station, for Precision Repair – a device designed for fast and precise work with SMD components. The DDE control unit is fully compatible with 10 tools and can simultaneously control two. It already comes standard with a T210 precision iron and AM120 adjustable micro tweezers, which allow quick and efficient work with a large portion of the components used in the industry. Also of great importance for the efficiency of this type of workstation are desoldering tools – such as the DEN-ON SC7000Z – which allow quick corrections to be made to the prototypes being created.
Devices
The next and undoubtedly the most important step is the selection of equipment included in the line. Small batch and prototype production is governed by the same principles and, as a rule, follows the same process as high-volume production, but taking into account the fact that the solutions used in it must allow rapid changes and a smooth transition from one assembly to another. The NEODEN line of equipment for prototyping and small batch production was developed for this purpose and with these objectives in mind. It allows small-scale implementation of all tasks normally performed on large industrial equipment.
Of course, the process begins with a stencil printer. In the type of production in question, handheld printers are already efficient and cost-effective. That’s why the well-established FP2636 model is included in the NEODEN product line under discussion. It is an easy-to-use device that allows high precision in the placement and thickness of paste application. At the same time, it allows for quick stencil changes, perfectly fitting for small batch operations. Of course, the printing process can be improved by using a semi-automatic device as an alternative. For small batch and prototype production, for example, the TWS SR-2700 stencil printer is an excellent choice. Its wide printing area – as large as 675 x 585 mm and first-class technical parameters make it an excellent value for money product.
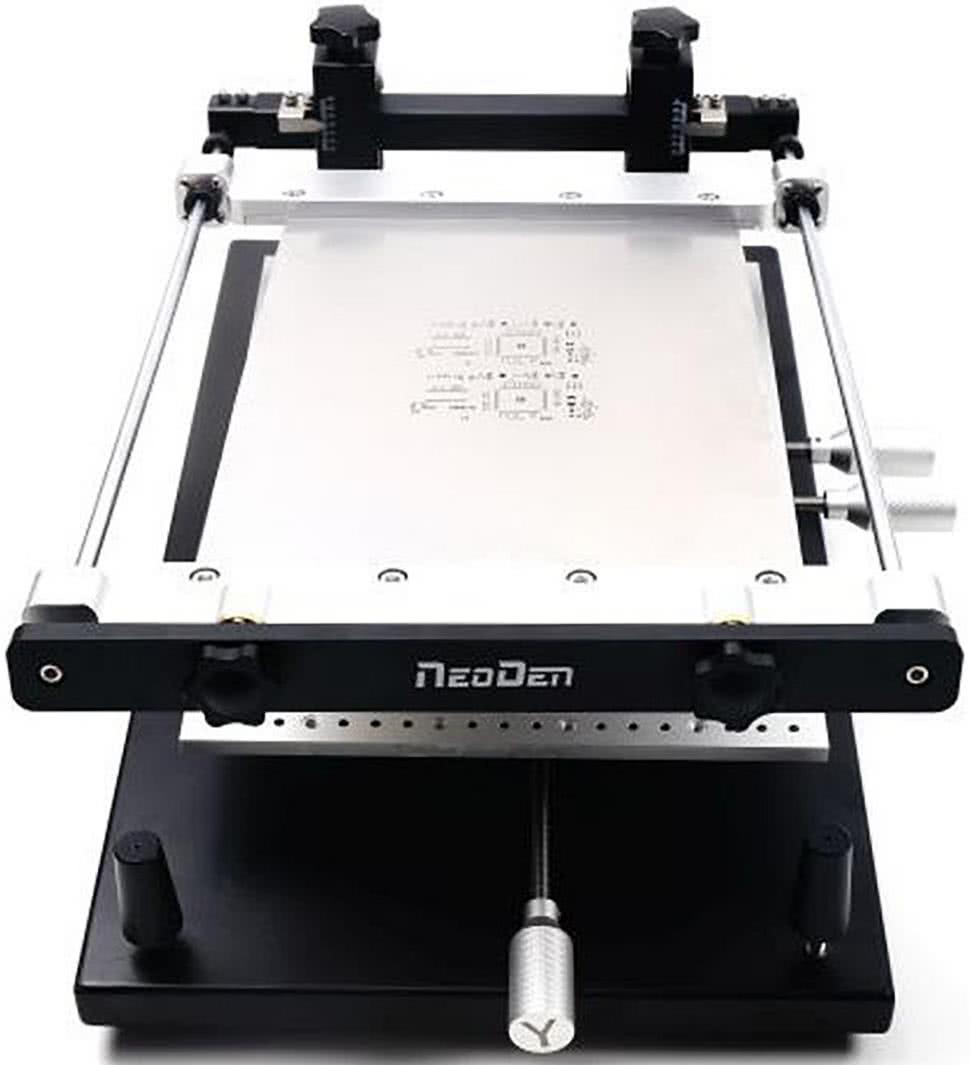
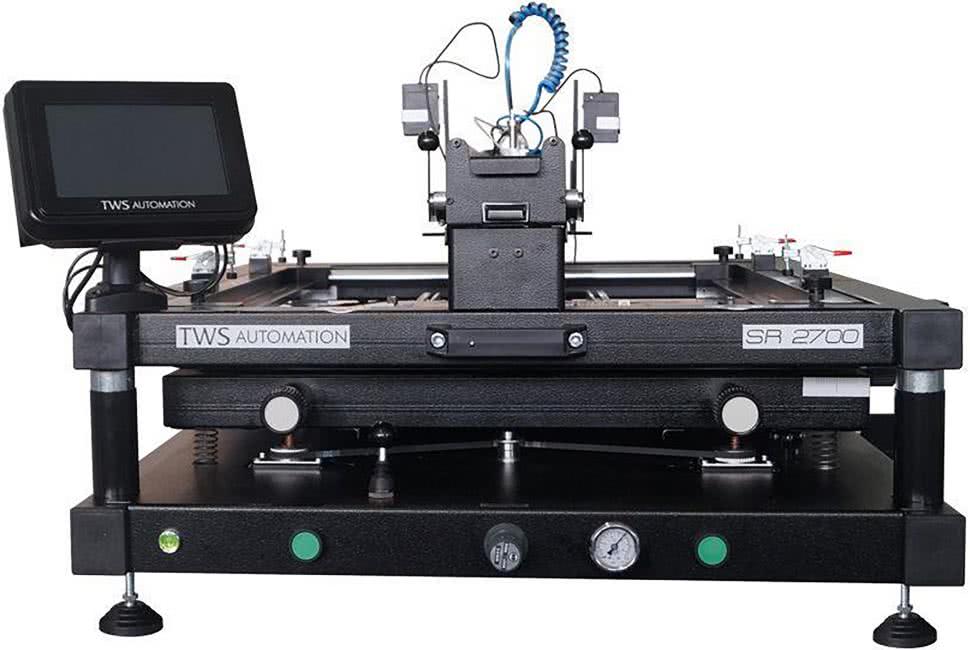
Two manually controlled cameras allow viewing when positioning the PCB against the stencil. The machine is equipped with two independent, self-levelling, pressure-controlled, electronically actuated squeegees and a system for automatically detaching the PCB from the stencil at a programmable speed. The maximum supported PCB thickness is as much as 6mm. Importantly for the frequent process changes characteristic of small batch production – the device is equipped with a touch-screen operator panel and is very easy to use.
The device is equipped with 4 mounting heads and allows working on PCBs up to: 350x400mm, and an additional option up to 310x1500mm, and with components in the range up to 0201 – 35x35mm. In doing so, the machine achieves a very good output of 4400CPH for small batch production and supports up to 48 8mm feeders. Considering the frequency of small batch production changes, the choice should take into account how quickly the device can be reconfigured to make the next batch of products. Using the NEODEN4 device as an example, it is clear that the intuitiveness of the software and the speed of physical reconfiguration of the device are crucial. Completing the lineup is, of course, a reflow oven. The model that fits into the discussed list of NEODEN devices is the IN6. The device is based on 3 heating zones and 1 cooling zone allowing it to realize profiles up to 300°C. An additional thermocouple allows for quick profiling and optimization, which enables a smooth transition from one product series to the next, meeting the requirements of small batch and prototype production. As an alternative, the larger – five-zone TWS AUTOMATION 1385 EVO can be used, equipped with K-type thermocouples placed in each zone. The oven is equipped with two types of transport: edge transport with central support and mesh transport in the range of 110 – 305 mm working at a speed of 100 to 500mm/min.
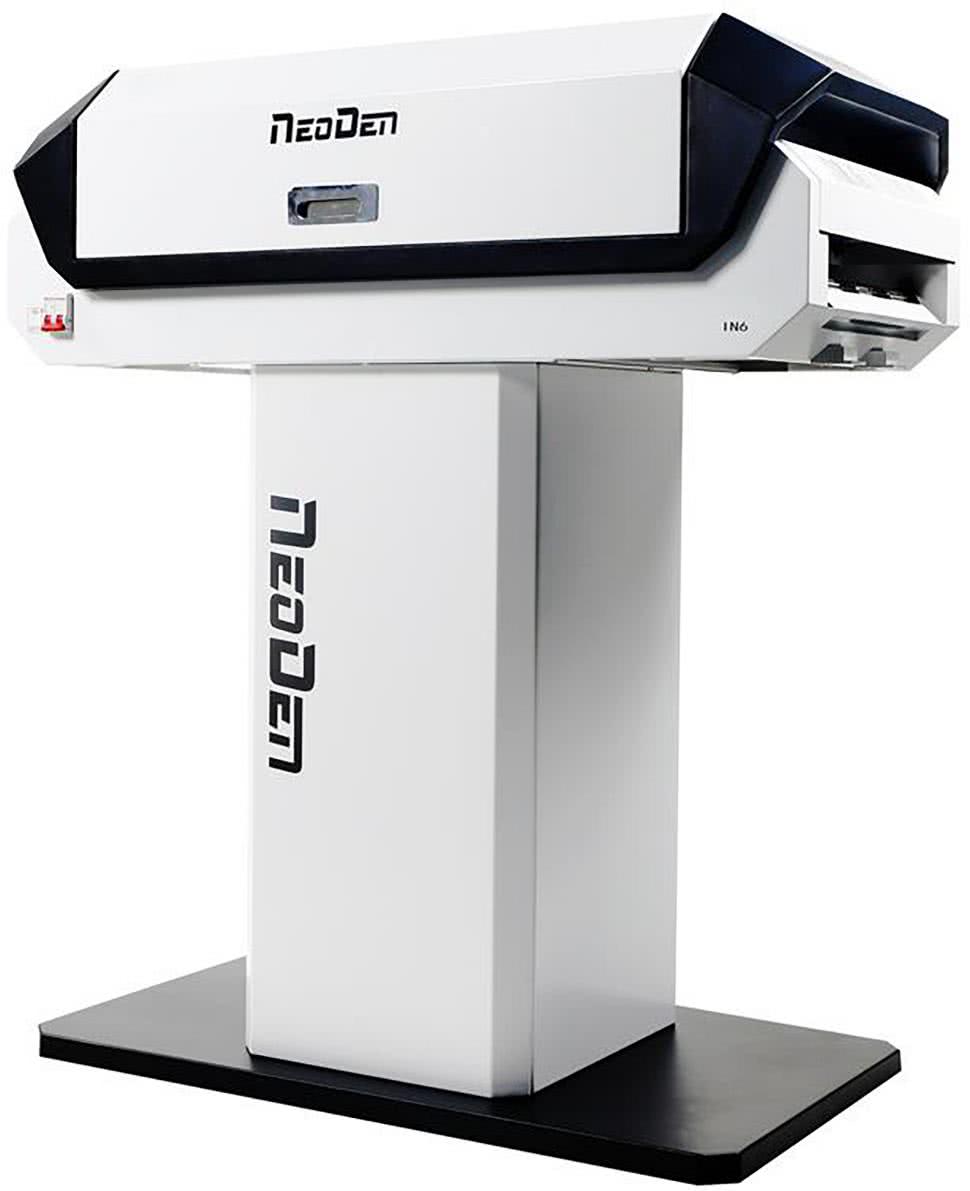
Stock Management
The issue of stock management should also be noted here. Small batch production, contrary to appearances, can be a much greater logistical challenge than high-volume production. This is because it often requires keeping in stock and handling a wide range of electronic components. Errors in this management process lead to downtime and, in the case of moisture-sensitive components (MSDs), material losses. The solution, can be to equip the back of the line with the right cabinets to protect electronic components. REECO Dehumidification Cabinets are an excellent example. This type of equipment provides and maintains the low degree of humidity necessary to keep components safe in accordance with IPC/JEDEC J-STD-033B.1 at less than 5% RH, with 2% RH being the standard value achieved. Of particular importance, the dehumidification modules in REECO products operate at all times, maintaining the required humidity level regardless of the correctness of the sensors. This provides additional protection for stored components in case the sensors fail. Ease of operation of the units is also a significant factor. Installation is limited to connecting the device to a power source and does not require any settings.
THT assembly
Completing the line are solutions to automate THT assembly. Conventionally, this process uses waves of solder. For small batch production, however, more cost-efficient are precision soldering robots, which do not require heating the entire crucible of solder and can be quickly reprogrammed from one batch realization to another. The best example of such a solution is the REECO Soldering Robot, the flagship model of REECO’s series of robots awarded with the TERAZ POLSKA emblem.
Summary
In addition to meeting the same requirements as for high-volume production, equipment components designed for low-volume production must allow flexible and rapid reconfiguration of the line.
The solutions discussed can be seen and tested at the RENEX TECHNOLOGY AND TRAINING CENTER. Its activities also include courses in the operation of equipment and entire production lines.
