Small volume production of electronics is governed by the same requirements as large volume production. It is necessary to maintain antistatic protection and to select the right tools and mechanisms of operation allowing for efficient and cost-effective production. What distinguishes them, however, is the flexibility requirement resulting from the nature of this activity and the ability to change series efficiently.
Taking into account the above, the design of a small scale electronic production line should start from the space in which the activity will take place. Due to the sensitivity of a large part of the components used in the industry, an ESD (electrostatic discharge) protective zone should be designated and appropriately equipped, which reduces the risk of electrostatic discharge losses. This applies to suitable flooring, furniture and equipment. Anti-static floors such as those of FORBO are available in the form of 60 cm fast-assembly tiles, which can be laid on any surface, so covering even a fairly large area and even its subsequent expansion is not a problem. An example of antistatic furniture designed for the production of electronics is the renowned in Europe Polish brand REECO. For small companies and those starting their business activity, Classic series tables providing antistatic security at prices much lower than those we will encounter in imported products may be a perfect solution. The possibilities of adjusting the workstation based on such a table are very wide – constructions of this type have a modular character – which allows for their flexible configuration for the needs of a given production line.
CLOTHING
Before we move on to the equipment, it is worth mentioning the often neglected element of the EPA zones – the appropriate staff clothing. Appropriate clothing, i.e. clothing with antistatic properties, should be treated as any other necessary piece of equipment. Practice shows that negligence in this respect is often the weak link that makes all efforts to properly create and maintain an EPA zone are nullified. In this case, REECO products are also worthy of recommendation. The range of antistatic clothing, again at competitive prices, is very wide here, allowing you to choose solutions tailored to your business.
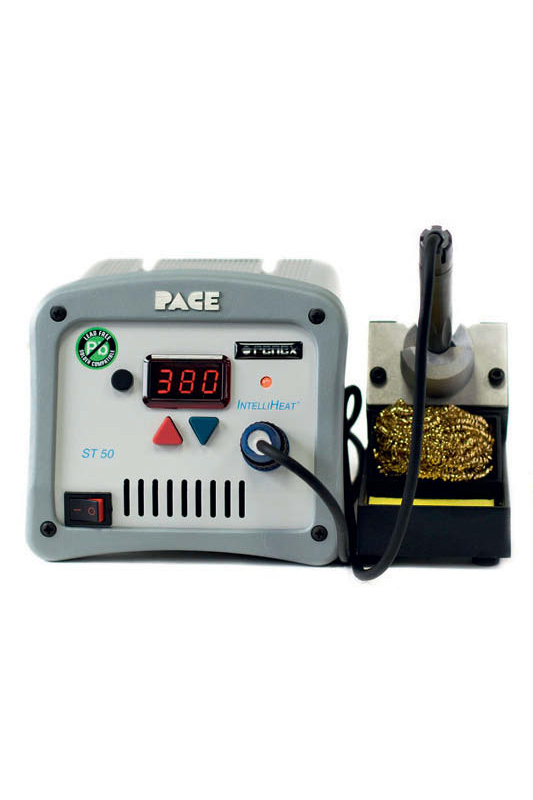
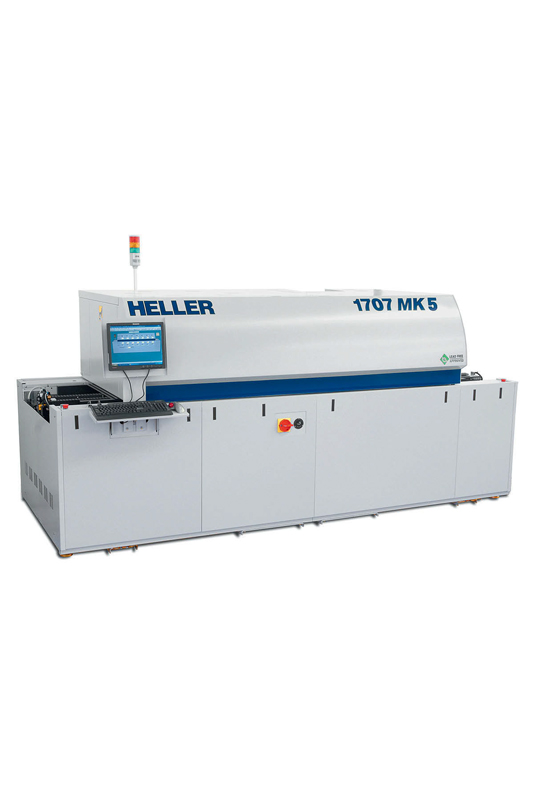
MANUAL WORKSTATION
Once the right protection is in place, focus on the tools and equipment. As we mentioned in the introduction, flexibility is the key to small batch production due to its specificity. The basis, apart from hand tools such as cutters and tweezers, is a good soldering station. Of great importance are therefore the ability to change the temperature of the soldering tip and a wide range of compatible tips quickly and preferably capability to programme them.
The work will be accelerated by stations equipped with several soldering handles with different tips, so that subsequent tasks can be performed without the need to adjust the tools. Such functions have e.g. Pace ST50 or WJS-100. Desoldering guns – such as DEN-ON SC7000Z – allowing for quick correction of soldered connections are also very important for the efficiency of the workstation.
EQUIPMENT
Going beyond the manual workstation, semi-automatic stencil printers such as GRP SR-2700 can be a good solution for small and medium scale production. These devices are equipped with two independent, self-levelling, pressure-controlled, electronically activated rakles, which allows for precise and very efficient distribution of soldering paste. At the same time, the device enables a quick template change, perfectly matching the specificity of small volume activities. The next step, and at the same time the production stage is the assembly of components on a PCB. This is done with the use of pick & place machines, such as the recently very popular and at the same time the fastest on the market (capacity of up to 31 thousand components per hour) Yamaha YSM10.
Again, with production flexibility, the choice must take into account how quickly the device can be reconfigured for the next product series. On the example of YSM10 we can see that intuitive software and speed of physical reconfiguration of the device (e.g. change of reels with components) are crucial here.
WAREHOUSE MANAGEMENT
Here, the issue of warehouse management should also be addressed. Contrary to appearances, small-scale production can be a much greater logistical challenge than large-scale production. It often requires a wide range of electronic components to be kept in stock and operated. Errors in this management process lead to downtime and, in the case of sensitive components (e.g. MSDs), to material losses. For this reason, warehouse management is based in modern companies on ERP (enterprise resource planning) solutions allowing for effective management of warehouse management processes. An example is the recognised IEMME solution LZERO 3.
This system is based on a protective cabinet and software that allows the quantity, location and flow of components and subassemblies in the production plant to be tracked. It should be noted, however, that storage locations can also be defined outside the cabinet – e.g. in the warehouse/ rack/shelf diagram. This allows you to manage not only electronic components, but also large components – such as housings.
As a result, the software allows you to track the inventory and flow of all components, not only those intended for the production of PCBs. The software also allows to obtain a full archive of data on the components used in a particular product (device), which allows, for example, to easily determine from which manufacturer the defective component came. Returning to the production line, the top of the line is of course a reflow oven. It is difficult to find a more recognized brand than the world leader in the production of these devices – Heller Industries and its “flagship” model 1707 MK5 equipped with 7 fully programmable heating zones and 1 cooling zone. The investment in this type of device will allow you to carry out any type of order and enable you to move smoothly from one product series to the next.
The line is complemented by solutions allowing automation of THT assembly. Soldering waves are conventionally used in this process. In the case of small volume production, however, more cost-efficient are precision soldering robots, which do not require heating of the entire solder crucible and can be quickly reprogrammed from one batch to another. The best example of such a solution is the REECO Soldering Robot, which many fans of sports soldering had the opportunity to see at various industry events in Poland and Europe competing with the champions in soldering. To sum up – solutions for small volume production, apart from meeting the same requirements as for large volume production, must allow for flexible and quick line reconfiguration. These solutions can be seen and tested at the Renex Group Technology Centre and demo room.