The progress in the production of electronic packages that we can see on a daily basis as consumers of devices such as telephones and TVs clearly shows the trend towards miniaturisation of electronic components and thus of the circuit boards themselves. This is possible thanks to the increasing number of SMD (Surface Mounted Devices) components used in electronic circuits. Small dimensions, flat cases and leads at the ends of the components allow, on the one hand, for the miniaturization of the assembled circuits, and on the other hand, for their increasingly faster production, thanks to the development of Pick&Place machines for laying the above-mentioned components on PCBs.
Unfortunately, at the current stage of development of technologies used in the production of electronic packages, it is not possible to completely eliminate the THT type components. We still need power connectors, large capacitors or power transistors, which due to their size or current values cannot be soldered in Surface Mount Technology (SMT). In the standard production process, the soldering of the THT type components is done on the so-called “wave”, due to the very high performance of these machines, but it also has its price. The process of soldering on a wave requires complicated carriers made of very expensive materials.
The carriers must also be made individually for each application that will be subjected to the “wave” soldering process. Due to increasing miniaturization, the selective soldering process is also used, in which the leads of components assembled using the through-hole technology are set on a narrow nozzle with a binder, so that only the places of interest are soldered, unfortunately, this process is much slower and much more complicated than “on the wave” soldering.
Recently, we have seen a growing market share of robots in electronics production. These are no longer highly specialized machines for the production of semiconductors or liquid crystal displays, but classic SCARA robots, as well as six-axis robots, adapted to the tasks previously done by hand during the production process of electronic packages.
In order to meet customers’ expectations of continuously reducing production costs and increasing quality and productivity, Renex decided to build a machine for selective soldering of THT type components using Omron’s SCARA robot.
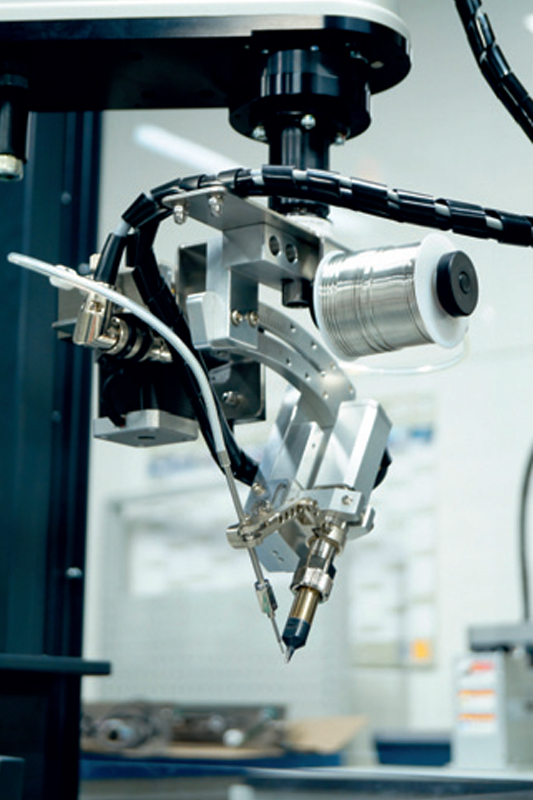
The basic assumption of the project was to avoid expensive carrier materials used in the wave process, to simplify the soldering process in relation to selective soldering, and the possibility of including equipment to work in production lines, based on in-line transport matching SMT production. Thanks to the experience that Renex has and cooperation with OMRON – one of the best suppliers of SCARA robots on the Polish market – the task was completed. In the second quarter of 2016 Renex will include in its offer a robotized station for soldering of THT type elements.
The machine is based on Renex’s frame design and Omron’s R6YXGL series SCARA robot. The machine is designed for conveyors, soldering head, automatic solder wire feeder, blade cleaning station and induction generator for soldering handle. Renex opted for 150W induction technology with a high thermal capacity, which allows to solder even very large heat sinks, which are not possible to solder with conventional soldering tools.
The automatic wire feeder is compatible with wires from 0.5 to 1.5 mm in diameter, both with and without a flux core. The wire feeder itself perforates the entire length of the wire, which significantly reduces the phenomenon of spattering flux and solder when they come into contact with a heated soldering tip. The device is equipped with conveyor and SMEMA interface, according to IPC guidelines (doc. IPC-SMEMA-9851).
Therefore, several devices can be assembled together if the application requires more than one tip or use loader and unloader stations to automate the feeding of parts into the machine. The whole process is handled by a PLC that controls all auxiliary equipment such as transport, soldering unit, wire feeder, tip cleaning station, and shows the current status of the machine on both Omron’s 7-inch NB-series operator panel and the Patlite signal tower of the same company’s LME series. A programmable relay compliant with the machine directive is responsible for safety and independently performs all safety functions used in the machine. For quick programming, Gerber files can be used that hold the design of the board from which we will point out the soldering points or use the method of pointing out points at the first detail and programming their position in the robot.
For programming, a PC with a dedicated software application is used. The application was developed by Renex using an Ethernet/IP interface. The machine itself does not require a PC to work, and once programmed, it carries out the process itself. The project will be further developed according to suggestions from customers and integrators working in the electronics industry. At the same time, we invite you to contact Renex regarding cooperation in the development of the machine and support during sales of product implementations. The partnership established with Omron and the support of the application engineers has allowed for a fast project implementation.
The success of the machine and the good reception of the first customers who took part in the testing of the machine will surely lead to a deeper cooperation with Omron on subsequent projects. RENEX is one of the largest and longest operating Polish companies, providing the latest technology in the field of production and service of electronics not only in Poland, but in the whole Central and Eastern Europe.
The range of products in the company’s offer is very wide – from small hand tools through soldering equipment, optical inspection, ESD protection, industrial furniture, to complete and fully automated production lines for the assembly of surface mounted components. Renex under its own brand REECO is a manufacturer of equipment needed by the electronics industry and not available from distributors worldwide. REECO is distributed throughout Europe through the company’s Romanian, Serbian and Croatian branches and a network of distributors in Western Europe, Renex is also the world’s largest IPC training centre for the electronics industry (3,000 people per year). We invite all integrators and sales companies to cooperate and visit our Technology Centre. On 2000 square meters you will be able to get acquainted with a variety of equipment used in the electronics industry – from hand tools to complete SMT lines.
DOWNLOAD PDF (IN POLISH)